Aluminium Die Casting
The entire Aluminium Die Casting process of manufacturing takes place in a well equipped facility with the latest HPDC machined like Buhler , Zitai , Yizumi , Chit-Shun Etc
The largest casting that is presently produced in our facility is about 2.2 Kgs . Our closed loop and real time control die casting machines provide for highly repeatable process with reduced casting rejections and are the most preferred equipment for some of our customers producing safety critical parts for the auto industry.
A Central melting Tower furnace of 500kg/hr capacity along with a couple of BT furnaces of 500Kg capacity provide for molten metal to each of the Electric holding furnaces near the die casting machines.
Post die casting operations like fettling and trimming are carried out by semi-automatic machines. Drilling is carried out a conventional machines using special fixtures to keep costs low.
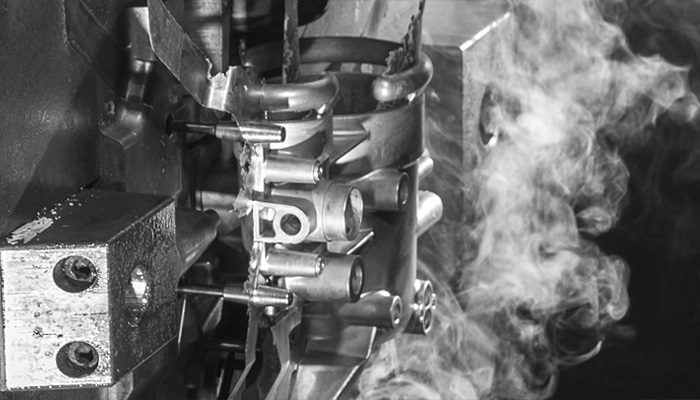
surface finishing operations like shot blasting and vibro finishing operations like shot blasting and vibro finishing are carried out in-house along with vacuum impregnation to supply pressure tight castings.
Followed by the Die casting and machining , Some the parts are getting chromating as well as powder coating as per customer requirements.
Using Hot chamber and Cold chamber Die-Cast technologies, along with standard and multi-slide tooling systems. Each of the alloys has unique Chemical and mechanical properties physical to meet out your specific application. We have a team of experts who will assist you to pick the right material to manufacture your complex geometry components.
We are specialized in manufacturing and supplying of Aluminum Casted parts in various process routes,
- High-Pressure Die Casting
- Low-Pressure Die Casting
- Gravity Die Casting
- Sand Casting
We make parts from few grams to large precision components in a broad range of
- Aluminum
- Zinc
Aluminum Alloy Characteristics
High operating temperature
Outstanding corrosion resistance properties
Lightweight
Flexibility in post-process like machining and Surface coating
Can cast low wall thickness to reduce the component weight.
Very good strength and hardness
Good stiffness and strength-to-weight ratio
Excellent in Electromagnetic interference (EMI ) shielding properties
Excellent thermal conductivity
High electrical conductivity
Good in surface finishing characteristics
Full recyclability
Aluminum’s strength, corrosion resistance, and heat-dissipating properties offer mechanical designers significant advantages. And our proprietary Thin Wall Aluminum Technology has made aluminum die casting an option for even more applications.
Advantages of Aluminum Die Casting
Economical process offering a wide range of sizes and shapes
One of the most significant benefits of aluminum die casting is that it creates lighter parts—with more surface finishing options than other die cast alloys
Cast aluminum is versatile, corrosion-resistant; it retains high dimensional stability
Can provide integral fastening elements as part of the design
CNC Machining can be used to further refine the design if needed
Aluminum Die Cast parts are strong and have a long life span
Complex shapes with high dimensional accuracy and stability than other mass production processes
Aluminum Die Cast parts can be manufactured with smooth or textured surfaces
Aluminum Die Cast parts can be easily anodized, painted or powder coated with minimal surface preparation
Various grade of Aluminum Alloys
High-Pressure Die Casting
A380 , A383 , A413, A360 , ADC1 , ADC 1Z
Low-Pressure Die Casting
A356, A413, AC2A, AC2B, AC4C, AC4A.
Gravity Die Casting
A356, A413, AC2A, AC2B, LM25, AC4A, Al-Si9Cu3.
Squeeze Die Casting
A380, A383.
Sand Casting
A356, A413, AC46200, AC2A.
Zinc
Zamak3, Zamak5, Zamak7
Magnesium
AZ91D, AM50A, AM60A
High Pressure Die Casting
We make HPDC components range from 25 Grams to 20 Kgs. We equipped machine range from 80 Ton to 3400 Ton Precision High pressure Die Casting Machines.
Most of the machines having a closed-loop operation, Automatic spray, Auto ladle, Auto extractor capabilities, where we can make the high precision and varied wall thickness parts with the desired quality level.
Every HPDC machine having to hold a furnace, where we can control the temperature and alloy properties very precisely.
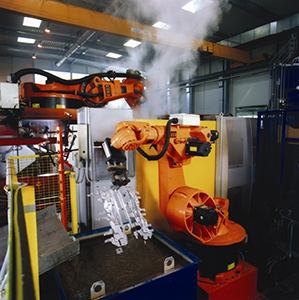
Low Pressure Die Casting
Low-pressure die casting is a method of production that uses pressure – rather than gravity – to fill molds with molten metal such as aluminum and magnesium. In this process, the holding furnace is located below the cast and the liquid metal is forced upwards through a riser tube and into the cavity
Gravity Die Casting
Our Gravity Die Casting capabilities includes Stationary and Tilting type GDC machines
We make GDC components range from 100 Grams to 100 Kgs.
We have the equipment to make the Shell Core for the comply casting profiles.
Followed by the GDC process, We perform Solution Heat Treatment & Precipitation Heat Treatment to achieve the mechanical properties
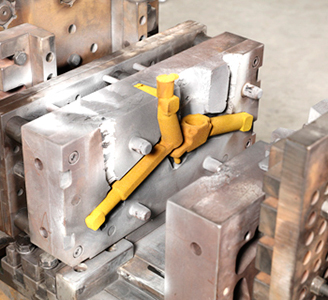
Sand Casting
We make Alu casting through the NO BAKE Sand casting process, where we produce parts from 10 Grams to 250 Kgs Kgs.
Extrusion
Extrusion is the process used to create lengths of aluminum of a fixed cross-sectional profile.
The process of aluminum extrusion works by forcing a block of metal, known as a billet, to pass through the die opening of the smaller cross-sectional area than the billet itself
Aluminum extrusion is a process for creating parts with specific cross-sectional profiles by pushing heated alloy material through a die.
Shapes created can be solid, hollow, and semi-hollow; and they can be simple or they can be complex.
The process of extrusion is an interesting one, resulting in 8-24 foot long profiles that can then be heat treated, finished, and fabricated to customer specifications.
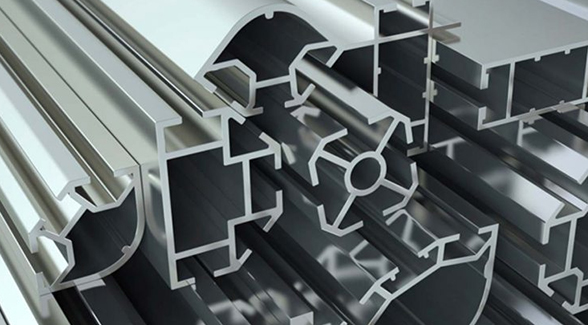
IS India(NEW) | (BS)U.K or I.S.(OLD) | (AA) U.S.A |
(AICAN) Canada |
DIN Dermany |
ASTM | (JIS) Japan |
(AFNOR) France |
Russia |
---|---|---|---|---|---|---|---|---|
19500 | E1B | 1050 or.1060 | IS | AI 99.5 | 99.6A | AI-1 | A-5 | – |
19000 | E1C | 1100 | 2S | AI 99.0 | 99.0A | AI-3 | A-4 | A-2 |
19501 | E1E | EC | CISDIA | E-AI99.5 | EC | AI-1 | – | – |
63401 | E91E | 6101 | D50S | E-AI-Mg.Si.O.5 | GS 10B | – | – | – |
– | NE-3 | 3103 | 3S | AI Mn | – | – | 3103 | – |
52000 | NE-4 | 5052 | M57S | AIMg2 | GR 20A | A2-SI | A-G3 | AM |
53000 | NE5 | 5086 | 54S | AiMg3.5 | GM 40A | – | – | – |
63400 | HE-9 | 6063 | 50S | AiMg Si0.5 | GS 10A | A2-S5 | A-SG> | – |
24345 | HE-15 | 2014 | B26S | AI-Cu-Si | – | – | – | – |
Temper Designation Table
INDIA or U.K | U.S.A or CANADA | ISO TEMPER | Description of designation |
---|---|---|---|
O | O | O | Annealed |
M | F | F | As fabricated, as manufactured, or as cast |
– | T3 | TD | Solution heat-treated and cold worked |
W | T4 | TB | Solution heat-treated, naturally aged, and amenable to artificial ageing |
P | T5 | TE | Artifically aged or precipitation heat-treated |
WP | T6 | Tf | Solution heat-treated & Precipitation heat-treated |
H-21 H-1 | H2A H1 | Strain hardened to the specified strength | |
H-22 H-32 | H2B H3B | 1/4 Harf Stabilized | |
H-24 H-34 | H2D H3D | 1/2 Harf Stabilized | |
H-26 H-36 | H2F H3F | 3/4 Harf Stabilized | |
H-28 H-38 | H2H H3H | Fully hard, stabilized |