Forgings
NA-Mfg has wide variety of Eco manufacturing production lines spread across its manufacturing locations. Na-Mfg is one of the pioneer manufacturer and suppliers of closed die hot forgings. All our forging lines are equipped with state of the art billet temperature control mechanisms. NA-Mfg, boasts of wide variety of production lines to cater to satisfy the variety of customer needs. NA-Mfg., has automated high speed production lines and also can take parts with small batch sizes. NA-Mfg, intends to be “One stop shop” for the custom make closed die forging requirements.
Our Eco manufacturing equipped with Mechanical Presses and Drop hammers, where we could able to produce high complex forging profiles ; Weight range from few grams to 100 kgs to the various applications .
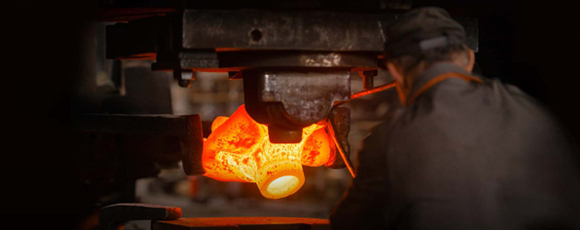
Availability and Productivity of the forging equipment are the key to sustainability. Production and Process controls are monitored using state of the art online production monitoring system. Periodic maintenance is carried out on a systematic manner to continuously improve the availability and productivity of the production lines.
Our forging lines are supported by various types of billet cutting equipments , which include saw cutting machines, shearing machines, circular saw machines and high speed shearing machines. Raw material bars of input Round sections and Square sections from 10mm to 180 mm diameter can be cut to accurate lengths and weights as required.
We follow FIFO of material from incoming storage to dispatch. The raw material grades are tracker by using unique color code from the incoming stage. By doing this practice, the parts quality is ensure all the stage. This provides end to end traceability of the components.
We provide the forging parts in various process methods
- Hot Forging ( Closed and Open Die )
- Cold Forging
- Ring Rolling
- Warm Forging
We make parts from few grams to large precision components in a broad range of grades of
- Ferrous
- Non- Ferrous
Hot Forging | Close Die Forging
The hot forging manufacturing process is performed at extremely high temperatures (up to 1150 °C for steel, 360 to 520 °C for al-alloys, 700 to 800 °C for cu-alloys). This temperature is necessary in order to avoid strain hardening of the metal during deformation.
We have capabilities of making Close die forged parts from few grams to 200 Kgs
We have equipped with Mechanical & Pneumatic hammer and Drop hammers
Continuous Hardening & Tempering Quench type Furnace.
Modern Hardening & Tempering Furnace with Polymer quenching Facility.
Annealing Furnace
Normalizing Furnace
Various grade of metal are heated by using medium frequency induction furnace and oil-fired furnace
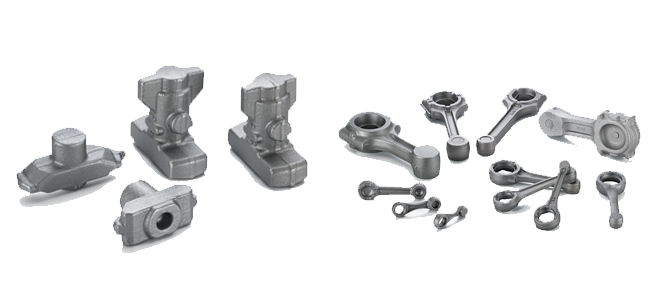
Weight Range: 150gms to 30Kgs
Material:
- Carbon Steel
- Alloy Steel
- Stainless Steel
- Brass
- Copper
- Aluminum
- Titanium
Hot Forging | Close Die Forging provides a variety of advantages
Lowers cost compared to other casting processes
High in productivity
Good in dimensional consistency
Lower tooling cost and Lead time than the other process
Can be produce casting from few hundreds to millions.
Forged steel is generally stronger and more reliable than castings and plate steel due to the fact that the grain flows of the steel are altered, conforming to the shape of the part.
The advantages of forging include: Generally tougher than alternatives. Will handle impact better than castings.
Hot Forging | Open Die Forging
We have capabilities of making open die forged parts up to 2000 Kgs
We have equipped with Mechanical Drop hammers
Manipulators are used to handling the heavy parts
Continuous Hardening & Tempering Quench type Furnace.
Modern Hardening & Tempering Furnace with Polymer quenching Facility.
Annealing Furnace.
Normalizing Furnace.
Various grades of metal are heated by using an oil-fired furnace.
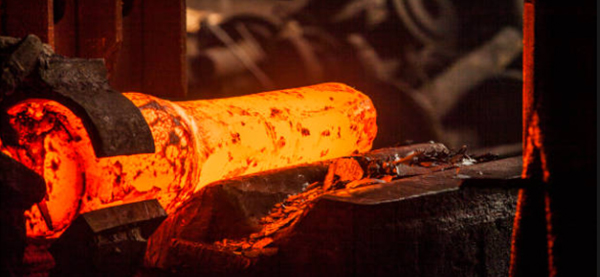
Weight Range: 10Kgs to 1500Kgs
Material:
- Carbon Steel
- Alloy Steel
- Stainless Steel
Hot Forging | Open Die Forging provides a variety of advantages
Greater mechanical properties.
Better fatigue resistance.
Improved microstructure.
Continuous grain flow and structure.
Finer grain size.
Lower tooling cost.
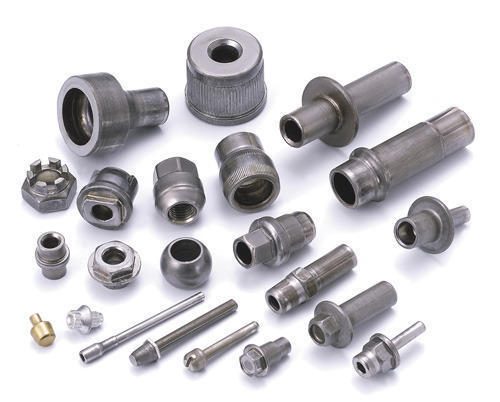
Cold Forging
The cold forging manufacturing process is performed at room temperature, without any thermal treatment. Cold forging is a manufacturing process where a bar-stock is inserted into a die after phosphating and squeezed with a second closed die. The deformation starts at room temperature and changes the shape and size of the initial part until it has assumed the shape of the die.
We have the capabilities of making Cold forged parts 4.0 Kgs.
We have equipped with Mechanical and Hydraulic screw up to 1000 ton.
Continuous Hardening & Tempering Quench type Furnace.
Modern Hardening & Tempering Furnace with Polymer quenching Facility.
Annealing Furnace.
Normalizing Furnace.
Various grades of alloys is using.
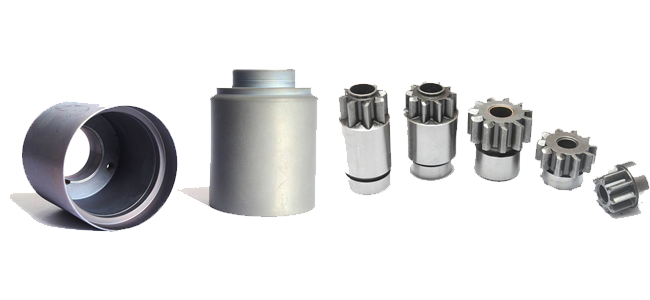
Weight Range: 10gms to 12Kgs
Material:
- Carbon Steel
- Alloy Steel
- Stainless Steel
- Brass
- Copper
- Aluminium
Cold Forging provides a variety of advantages
The major advantages of cold forging are close dimensional tolerances.
Good surface finish quality.
The use of lower-cost materials to obtain the required strength by work hardening without requiring heat treatment.
Greater mechanical properties.
Ductility and fatigue and impact resistance because this process refines and directs the grain flow according to the shape of the piece.
Almost all metals—ferrous and non-ferrous— can be forged. Any kind of steel can be used: carbon, alloy, stainless, or superalloy.
Ring Rolling
Ring rolling is a category of metal rolling, in which a ring of smaller diameter is rolled into a precise ring of larger diameter and a reduced cross-section. This is accomplished by the use of two rollers, one driven and one idle, acting on either side of the ring’s cross-section.
We have capabilities of making Ring rolling pats unto 1000 mm in OD and 200 mm on thick.
Continuous Hardening & Tempering Quench type Furnace.
Modern Hardening & Tempering Furnace with Polymer quenching Facility.
Annealing Furnace.
Normalizing Furnace.
Various grades of alloys are using.
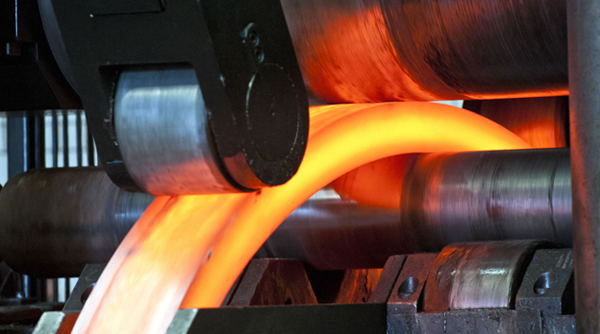
- Maximum Diameter: 1000mm
- Maximum Wall Thickness: 150mm
- Maximum height: 600mm
Material :
- Carbon
- Steel Alloy
- Steel Stainless Steel
Ring Rolling provides a variety of advantages
Continuous production of forged products with a very short cycle time and high production rates is suitable for mass production.
Improved grain flow.
Better surface finish and breakdown of scale in steel forgings.
Good surface finish quality.
Warm Forging
Warm forging is performed with the workpiece heated to a range that is generally above the work hardening temperature and below the temperature at which scale forms. The process fills the niche between the closer tolerance, but sometimes expensive cold forging process and the somewhat lower precision hot forging process. It is being used to produce close tolerance components in steel alloys that were not feasible or impossible by cold forging. It is also being used to produce components very close to the final shape that was formerly made by hot forging with generous finishing allowances. Shafts, gears, and automotive front-wheel drive tulips are currently being warm forged.
The cold forging manufacturing process is performed at room temperature, without any thermal treatment. Cold forging is a manufacturing process where a bar-stock is inserted into a die after phosphating and squeezed with a second closed die. The deformation starts at room temperature and changes the shape and size of the initial part until it has assumed the shape of the die.
We have the capabilities of making Warm forged parts 3.0 Kgs.
We have equipped with Mechanical and Hydraulic screws up to 1000 tons.
Continuous Hardening & Tempering Quench type Furnace.
Modern Hardening & Tempering Furnace with Polymer quenching Facility.
Annealing Furnace.
Normalizing Furnace.
Various grade of alloys is using.
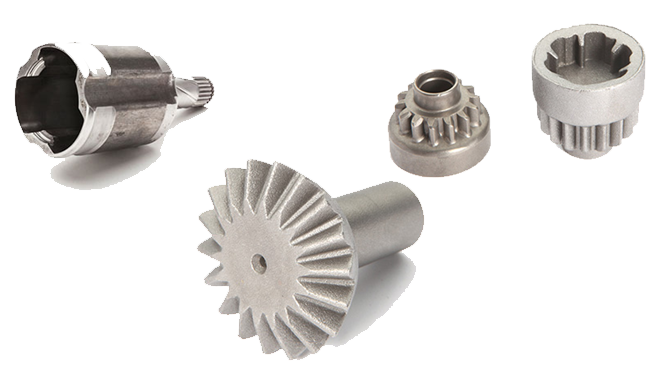
Weight Range: 0.5Kgs to 15Kgs
Material :
- Aluminum
- Brass
- Copper
- Carbon Steel
- Alloy Steel
- Stainless Steel
Industries we serve
Our Forging Capabilities Include
Casting are produced according to IS 8062
ISO:9001 & IATF 16949:2016 Certified
Mould flow simulation
Casting tooling , Fixtures and Gauges
Precision Machining
Part Pressure washing
Sophisticated Chemistry and Mechanical lab
Jominy end quench testing facility
Stress relieving , Heat treatment , Quenching & Tempering
Radiography and Destructive testing
Lean Manufacturing
Engineering Assistance , 3 D Scanning , Rapid Prototype & VAVE
Quality Audits
Global Logistics Management
JIT & KANBAN
Assembly, Painting & Anodizing
Warehousing & Inventory Management