Iron Casting
We cater Iron casting parts in various process methods
- Green Sand Casting
- Shell Casting
- NO BAKE Casting
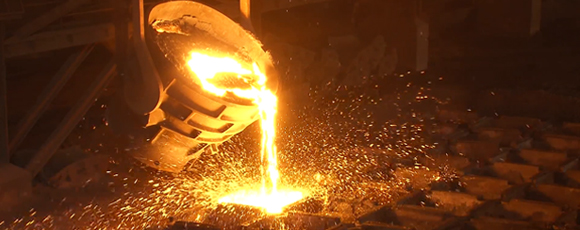
We make parts from few grams to large precision components in a broad range of grades of
- Gray Iron
- Ductile Iron
- Compacted Graphite Iron ( CGI )
- Austempered Ductile Iron (ADI )
- Silicon molybdenum ductile cast iron (Si-Mo )
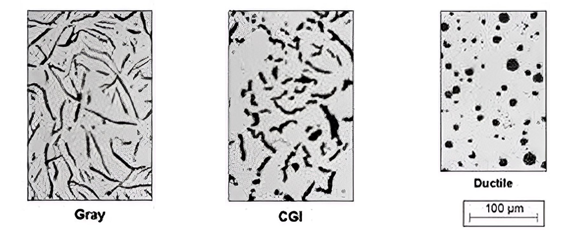
Green Sand Moulding
Flask Size
- Min : 400 x 400 x 150(x2) mm
- Max : 1300 x 1100 x 350(x2) mm
Material Grades | |||
---|---|---|---|
Grey Iron | Ductlle Iron | ||
Grades | Standards | Grades | Standards |
#20 #25 |
ASTM A48 | 60-40-18 60-42-10 |
ASTM A536 |
#30 | DIN 1619 | 65-45-12 70-50-05 |
DIN 1693 |
#35 #40 |
EN 1561 | 80-55-06 100-70-03 |
EN 1563 |
Shell Moulding
Flask Size
- 350 x 350 x 100(x2) mm
Material Grades | |||
---|---|---|---|
Grey Iron | Ductlle Iron | ||
Grades | Standards | Grades | Standards |
#20 #25 |
ASTM A48 | 60-40-18 60-42-10 |
ASTM A536 |
#30 | DIN 1619 | 65-45-12 70-50-05 |
DIN 1693 |
#35 #40 |
EN 1561 | 80-55-06 100-70-03 |
EN 1563 |
Green Sand Casting
We make iron castings from 250 Grams to 120 Kgs through High Pressure and Jolt Squeezing green sand molding.
In High-Pressure molding, We have equipped with Vertically and Horizontal parted molding lines.
We equipped molding machines to range from 20” X 24” to 40” X 48” where we make simply to high complex profile castings.
We have supporting capabilities that include Cold box Amin core, Silica sand Shell cores, and Resin coated cores, which are selected according to the part configuration, Complexity, and quality requirements.
Various grades of molten metal are prepared by a medium frequency induction furnace.
High-pressure molding line having integrated Auto pouring system and Jolt Squeezing line having monorail pouring method.
Green sand molding provides a variety of advantages
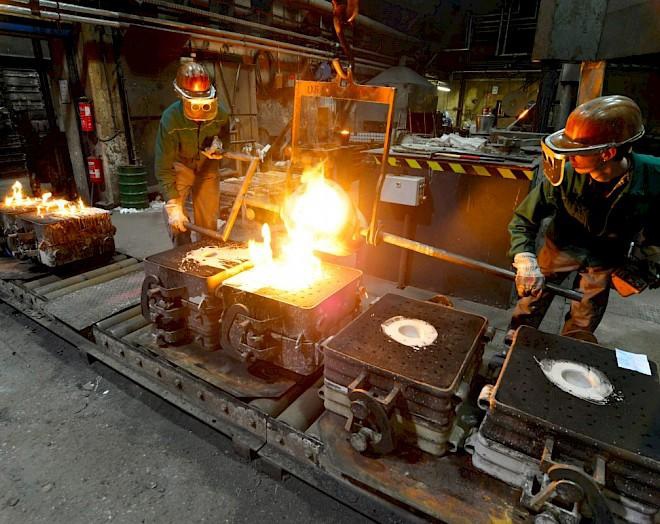
Lowers cost compared to other casting processes.
High productivity.
Good in dimensional consistency.
Lower tooling cost and Lead time than the other process.
Can be produce casting from few hundreds to millions.
Ability to produce both prototype and production volumes with the same process.
Provides a variety of molding processes to suit specific volume and quality requirements.
Shell Casting
Shell casting, also known as shell-mould casting is an expendable mould casting process that uses resin-covered fine silica sand to form the mould. As compared to green sand moulded casting, this process has better dimensional accuracy and a superior surface finish.
Shell Mould Preparation – First, each pattern half is heated to 175-370 °. Next, the heated pattern is clamped to a moulding station, which contains a mixture of sand and a resin binder. The moulding stations are inverted, allowing this sand-resin mixture to coat the pattern. The heated pattern partially cures the mixture, which now forms a shell around the pattern. Each pattern half and the surrounding shell is cured to completion in an oven and then the shell is ejected from the pattern. The two halves of the shell mould are secured together and the metal is poured into the shell to form the part. Once the metal solidifies, the shell is broken.
We produce Grey Iron, Ductile Iron, and ADI castings from 100 Grams to 20 Kgs.
We are equipped with single-station and multi-station Shell casting machines.
We have insert molding capabilities.
Various grades of molten metal are prepared by medium frequency induction furnace coupled with online Chemistry verification equipment.
Shell Moulded casting delivers a variety of advantages
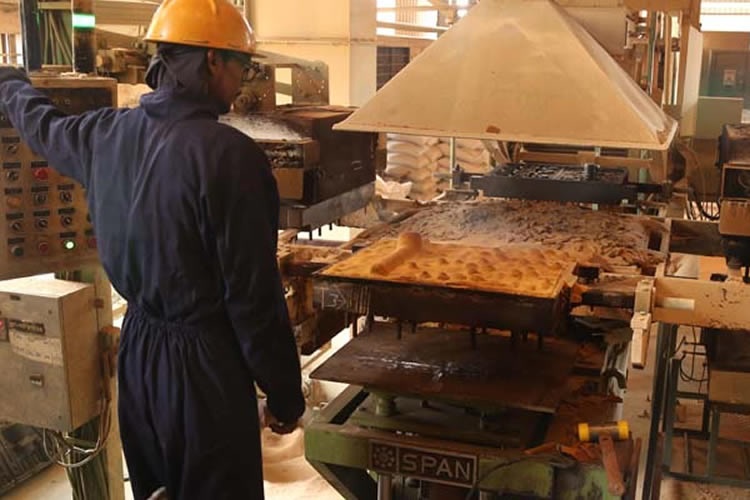
- Good in dimensional consistency
Highly complex cored profile casting can be produced
Low machining allowance
Good in Surface finish and aesthetics
Can be produce casting from mid to high volumes range
Draft Allowance: Typically 1°C
No BAKE Casting
No-bake moulds are also known as Resin sand casting. No Backcasting is expendable sand moulds, similar to typical sand moulds, except they also contain a quick-setting liquid resin and catalyst. Rather than being rammed, the moulding sand is poured into the flask and held until the resin solidifies, which occurs at room temperature. This type of moulding also produces a better surface finish than other types of sand moulds Co2. Because no heat is involved it is called a cold-setting process.
No BAKE casting’s advantages
Possibility of obtaining very complex geometries
Small and Midsize batches production
No limitation on the size of the part due to mold size
Molding flask can be fabricated according to the part profile
Austempered Ductile Iron [ADI]
provides a range of high-strength irons with higher ductility and toughness. Through the work hardening characteristics of the matrix, these irons have an exceptional blend of wear properties and toughness. These irons have the advantage that the base iron is readily machinable before heat treatment allowing hard wearing close tolerance and mating parts to be produced.
Our Iron Casting Capabilities Include
ISO:9001 & IATF 16949:2016 Certified
Mold flow simulation
Casting tooling, Fixtures, and Gauges
Precision Machining
Sophisticated Chemistry and Mechanical lab
Stress-relieving , Heat treatment, Quenching & Tempering
Engineering Assistance, 3 D Scanning, Rapid Prototype & VALVE
Quality Audits
Global Logistics Management
JIT & KANBAN
Assembly, Painting & Anodizing
Warehousing & Inventory Management